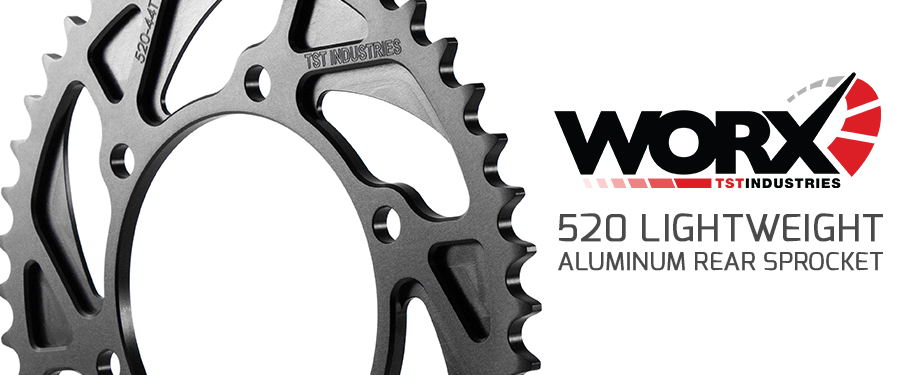
TST WORX Lightweight Aluminum Rear Sprocket – The Obvious, Yet Long Awaited Product From TST WORX
You’re probably sitting there thinking to yourself, “what the hell took you guys so long!? It’s literally IN YOUR LOGO!” We know, we know! But kind of like how Eggo took forever to make syrup, we took forever to make the thing that’s in our logo. We’ve been the go-to place for the brightest integrated tail lights, sleek fender eliminators, crash protection, LED signals, and now race components designed from our WORX race program, but we’ve never been the place to go to for a rear sprocket (though you wouldn’t think that by looking at our logo)….until now.
Let’s ignore the fact that Bart, TST Industries owner and operator, has a big sprocket tattoo on his leg, and focus on our racing efforts. As you probably know, we won the Moto3 ASRA National Championship last year (if you don’t know about it, CLICK HERE to read the story). In our quest for podium performances, we engineered and manufactured a lot of new components that were lighter, stronger, and performed better than their stock counterpart. We’ve passed these products along to our customers via the TST WORX Pack, and many of you may have thought that that was the end of it. On the contrary, that was just the beginning.
Getting to this point was a long road, probably a lot longer than you may be thinking. Things got really serious over two years ago, quickly turning something we’ve always talked about into a real plan with a solid goal, which was simple really; make it incredibly light, smooth, durable, and look cool as hell. Bart tackled the design and produced a sprocket model that provides all of the features previously mentioned, with an extra dash of badassery tossed in. The proprietary tooth profile and ultra-smooth tooth transition geometry leads to less frictional power loss, while the webbed design enables an incredibly lightweight and durable build. It has all of the makings for a top-level sprocket, but actually making it was another hurdle we had to jump.
We’ll be the first to tell you that it’s pretty easy to CNC machine a rear sprocket out of aluminum if you have the right tools. That rear sprocket won’t be the best quality possible, but it might do okay at its job, at least for a bit. It’s a whole different thing to machine a 7075-T6 aluminum alloy rear sprocket and ensure incredibly strict tolerances are met to provide the absolute best sprocket and material quality possible. Can you guess which route we took? We chose the latter. We had to figure out a way of manufacturing each sprocket in a way that eliminated even the tiniest vibrations caused by the machining itself, then come up with the best solution for anodized hardening to increase the raw materials durability and strength characteristics. This pursuit led us to develop our own proprietary holding plate technology used during the CNC machining process that inhibited those vibrations and enabled us to have precise control over the material removal. We optimized the coolant, tool paths, feed rates, and process parameters to limit material cold working and work hardening.
The anodizing process needed to match the level of quality we put into the machining. Don’t get us wrong, the raw 7075-T6 aluminum alloy is incredibly strong on its own, but we are chasing legendary status of hardening….like if you were to give a rear sprocket 100x the legal dose of gas station “performance” pills and see what happens. That’s why we chose to treat the entire sprocket with a black Type III hard coat anodized finish. For those not aware, this treatment penetrates the aluminum substrate and builds a micro-thin layer outside the substrate to form an ultra-hard and abrasion-resistant surface. Plus, the black finish looks amazing.
All of that is awesome, but you may still be thinking “why do I need an aftermarket sprocket…isn’t the stock one good enough?” That’s a valid question, but remember that “good enough” doesn’t win championships. That’s why you don’t see bone stock bikes competing in WSBK or MotoAmerica. ‘Good enough’ is nothing more than a balance of quality and performance determined by the bean counters at the manufacturer. They choose the option that will be the cheapest to produce and still provide enough performance to not drastically take away from the overall goal of the bike – not what is the best (translate that to most expensive to produce) option for bike’s performance. That usually means you get stuck with a heavier steel rear sprocket from the factory because they are cheaper to produce and relatively durable – a perfect balance for the accounting department. Remember, the rear sprocket is one of the main rotating forces in the drivetrain responsible for delivering power from the engine to the road, and having heavier components within that system will vampirically drain that power before it gets a chance to even hit the asphalt. You reduce the weight in that system and you increase the power at the wheel, as well as increase brake efficiency, it’s that simple. Ignoring the performance benefits and increased durability for a second, that black rear sprocket with the webbed design really sets off that section of your bike in a way that makes the stock sprocket stick out as a design oversight.
We wanted to ensure that our sprockets were built to handle every riding condition you could throw at it, which is why we repeatedly tested sprockets on a wide range of bikes for thousands of miles both on the street and on the track. Like I said previously, our Moto3 ASRA National Championship winning R3 Superbike was outfitted with one of the prototypes while it dominated the podium. We also mounted one to Mark Lourido’s Yamaha MT-07 and let him rip around on his bike to see what kind of damage he could inflict. After 4,000 miles, the answer is pretty obvious by looking at the picture below – none. You wipe the chain lube off and the teeth look brand new.
We specifically went the extra mile during design and production to build a sprocket capable of handling the harshest racing conditions. The result you see available today was truly bred and born through the fire of racing. It was made to handle the extreme load cycles of the track, quick shifters, rapid downshifts from redline, and the kind of lean angles that demand elbow pucks. The blend of material, design, proprietary tooth profile, ultra-smooth tooth transitions, and extremely durable anodized coating ensures exceptional performance at an ultralight weight that’s truly capable of increasing component performance on the track and street.
I think the most important thing here is that at the end of the day, after all the blood, sweat, and tears that went into the development, testing, manufacturing, and even more testing, is that our logo now makes a little more sense. Now only if you could figure out what TST stands for (spoiler – we’ll never tell).
If you want to get yourself a sprocket designed and manufactured by true race engineers with top-quality performance and longevity in mind, CLICK HERE and navigate to your specific motorcycle to see if we have one for your bike. We are adding support for new models every month, but if we don’t have one for your bike, drop a comment below and let us know what bike you have! We are always looking for input from our customers.
Mark L here to say I approve of this message! I currently have a 45tooth on and can’t wait to see how long it’s going to hold up. ?? Happy brapping!! ???
Please make for the 2020 ZX-6R. I have been looking for a superior sprocket that also looks good!